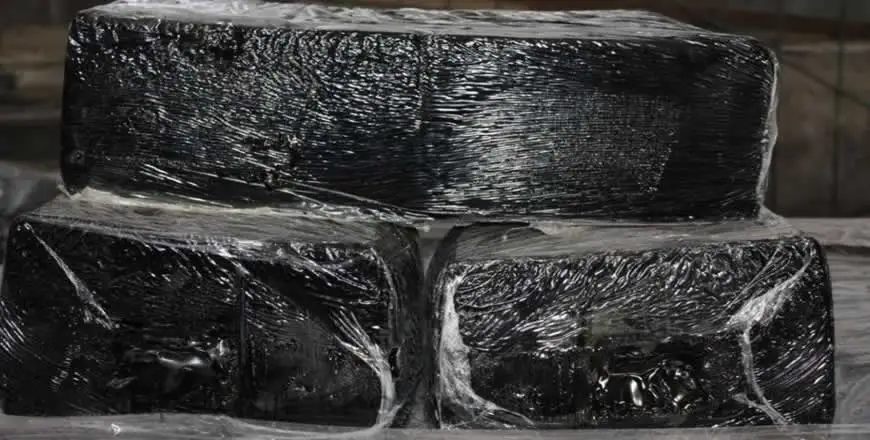
Oxidized Bitumen 90/10
DESCRIPTION OF OXIDIZED ASPHALT 90/10
Oxidized Bitumen 90/10 (in another word, oxidized bitumen 90/10, blown bitumen 90/10) is Semi Solid grade of pure petroleum bitumen manufactured by air-blowing through an asphalt flux. Special physical properties of its grade can be used in different applications in the construction business. Oxidized asphalt 90/10 is based on petroleum bitumen which is made by oxidized asphalt 60/70 by hot air. The numbers relate to the midpoint of the material’s softening point and penetration respectively. The softening point value is the degrees Centigrade measured by the Ring and Ball method as determined by ASTM D36. The penetration value is in 1/10 mm as determined by IP49 or ASTM- D5. Oxidized asphalt 90/10 with the arrangement of the international inspector to check quality and quantity of the Oxidized asphalt 90/10 during the loading to the vessel and controlling the production by QC by batch test report before shipping.
BLOWN ASPHALT 90/10
The foregoing Table sets out the characteristics of several 85-100 pen asphalt cements. As mentioned above, in various countries, asphalt cements are graded by penetration. In other countries, such as the United States, asphalts are graded persuant to viscosity. Asphalt precursors may be categorized, not only by penetration, but also by viscosity. Accordingly, in reference to ASTM standards, a “high quality paving asphalt precursor” is a vacuum tower bottom residue from refining of crude or crude blends suitable for production of paving asphalt cements meeting the requirements specified in ASTM D-3381, Table 2. A “low quality paving asphalt precursor” is a vacuum tower bottom residue from refining of crude or crude blends which are not suitable for production of paving asphalt cement meeting requirements specified in ASTM D-3381, Table 2, but are suitable for production of asphalts meeting the requirements specified in ASTM D-3381, Table 1. Further, a “non-paving asphalt precursor” is vacuum tower bottom residue from refining of crude or crude blends which are not suitable for production of asphalt cement meeting the requirements specified in ASTM D-3381 Table 1 or Table 2. High quality paving asphalt cements may be obtained by careful selection of the crude oil from which the asphalt cement is to be made and the operating conditions used to obtain the vacuum tower bottoms. By making an appropriate selection, a high quality paving asphalt cement may be obtained. Such crude oils and operating conditions are known to those in the art. For ease of reference such VTB and similar materials which may be used as a high quality paving asphalt cement or from which a high quality paving Oxidized bitumen 90/10 is obtained comprise the high quality paving asphalt precursors. Conversely, those paving asphalt precursors from which a high quality paving asphalt cement may not be obtained are referred to hereinafter as “non-high quality paving asphalt precursors”. Similarly, those VTB and similar material from which a lower quality paving asphalt cement is obtained or which may be used as a lower quality paving asphalt cement comprise the low quality paving asphalt precursors. Non-high quality paving asphalt precursors include low quality paving asphalt precursors and non-paving asphalt precursors.
RAHA OIL Bitumen Oxidized 90/10 is widely used as an anti-slip layer compound in the piling industry, for the manufacture of roofing felts, the roofing and waterproofing industries, for sound dampening felts and under carriage sealant in the automotive industry, electric cable joint protection, joint filling compound, carpet-backing, corrosion protection, acoustic panels, chemical, fuel, Manufacture of paints, sealant compound, and many others. Also used in sealing saw cuts and joints where expected movements are minimum. It is also used in the manufacturing of bituminous marine mastic for the oil & gas pipeline joints. Further, Oxidized Bitumen is used in the manufacture of bituminous marine mastic, which is required for the oil and gas pipeline joints.
- Oxidized bitumen is used as sealing of expansion joints.
- Oxidized bitumen is used as repair of joints or cracks.
- Oxidized bitumen is used as fixation of parquet floors.
- Oxidized bitumen is used as adhesive to be used in thermal insulation.
- Oxidized bitumen is used as repair of unexposed cracks.
- Oxidized bitumen is used as bonding of wet briquettes
- Oxidized bitumen is used in various industries like roofing, isolation, insulation flooring, mastics, pipe coatings, electrical applications.
APPLICATION OF BLOWN ASPHALT 90/10
Oxidized Bitumen 90/10 is a dark industrial Bitumen. Petroleum residue modified by the oxidation process. In addition, Blown Bitumen is produced by passing air through bitumen under controlled temperature state. Its stability ranges from highly viscous to solid. Blown bitumen grade has technical advantages such as durability, flexibility, water resistant and chemical stability. There is also the different grade of blown bitumen.
- Processing should be done from the bottom of blowing tanker. The reaction between oxidized bitumen and air is thermal. If Temperature produced during the mixture is high, it controlled by water injection.
- Mixing of air also the volume of blowing air are 2 main variants in the blowing method. oxidized bitumen made by blowning bitumen 60/70.
For oxidized bitumen 90/15 or 85/25 used or crude oil must be injected, according to volume 20-25. Otherwise, bitumen fragility results in inferior production. - Increasing heating temperature, air injection, time and tower pressure increase speed of output method reaction. Furthermore, the suitable temperature for production operation is 265-270 °C which must be controlled. So temperature doesn`t up because in 288 °C intensity of reaction becomes more sever and in-controllable that lead to the explosion in the tower.
- Bitumen shouldn’t stay in the tower and better is that delivered to drum or empty tanker soon.
- If the liquid surface in the blowing tower is low, adding more than a particular limit maybe lead to ignition. Also keeping high temperature may cause the same result.
- Fill up blowing tower to 70th. Air injection finishes at 190-232°C. Finally, sampling and testing product properties. Product temperature must be kept 150- 165 °C to loading and packing capability.
TECHNICAL ADVANTAGES OF BLOWN ASPHALT 90/10
- Durability
- Flexibility
- Water Resistant
- Chemical Stability
Compared to paving grade bitumen:
- Reduced temperature susceptibility
- Exhibits a more ‘solid’ nature at ambient temperatures
- High penetration index
STORAGE AND HANDLING
Heating of packaged bitumen is a critical phase in most of the final uses. Typically, the packaged material is heated and melted in boilers out on site. However, control at the heating phase is very important in terms of health and safety as well as in maintaining the quality of the product. Note must be taken of the maximum safe handling temperature of 230 C and this should not be abused. Bitumen is a poor conductor of heat, consequently, control of the heating phase is of paramount importance. The Blown Bitumen material should be broken up prior to placement in the boiler. This exposes a larger surface area to the heat and encourages a more even heating regime. Without the larger exposed surface area, aggressive heating at the base and sides of the boiler may well result in localized overheating, altering the characteristics of the RAHA OIL bitumen and potentially causing thermal cracking of the bitumen, creating the release of low lash vapors. The flash point of the oxidized bitumen then becomes irrelevant; as these low flash vapors determine the fire risk. Melted bitumen should not be left in the boiler and reheated from cold, as there is then a high potential for localized overheating around the heating area (lack of convection means poor heat transfer) and potential development of a pressurized pocket of low flash vapors. Be aware of the placement of any temperature monitoring or control devices. As a result of the poor thermal conductivity of the bitumen, a thermometer in the bitumen some distance from the heat source could read significantly different (even hundreds of degrees) from the true temperature of the bitumen near the heat source.
For Health and Safety information, please make reference to the relevant MSDS.
HEALTH & SAFETY
Workers should wear protective masks, gloves, and goggles during application. The asphalt can be removed from equipment and tools with kerosene or gasoline. Care should be taken when heating Blown Bitumen 90/10 to avoid over heating.
PACKING OF BLOWN BITUMEN 90/10
Oxidized Bitumen 90/10 in various packing, including Oxidized Bitumen 90/10 is available in 20 & 50 Kg Kraft Paper Bags 25 Kg Carton box & 200 Kg Steel Drums:
25 KG CARTON BOX
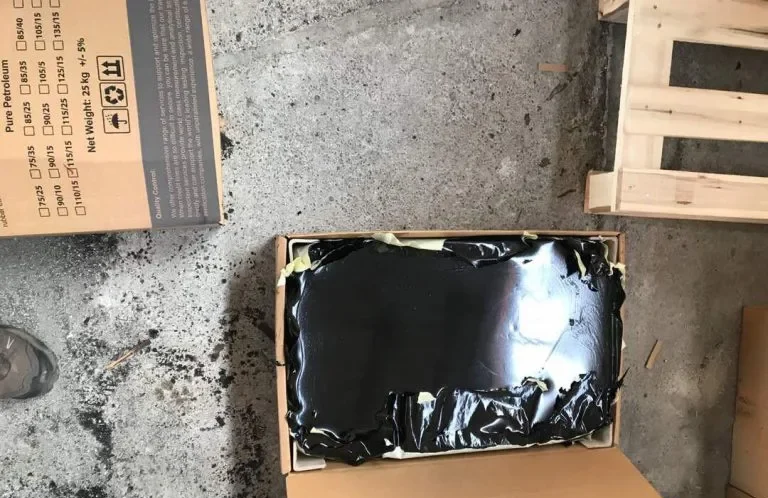
25 KG MOLD PACKING: It is most expensive packing since there is mold on and with same mold we can ship out. The mold is carton and at destination you can remove the mold easily.
25 KG POLYAMIDE BAG: It is heat resistance bag and filling directly in water to cool down fast. It is firstly use not possible to take out the Polyamide from the bitumen and then use.
25 KG CRAFT BAG: Craft bag is recycle packing and inside is special material to prevent sticking the bitumen to bag. This grade also possible to load on pallet or without pallet for customer.
TECHNICAL DATA SHEET OF BLOWN BITUMEN 90/10
BITUMEN 90/10 TEST METHOD UNIT SPECIFICATION
Specific gravity @ 25/25 °c ASTM D70 Kg/cm³ 1.05 approx
Penetration @ 25°c ASTM D5 mm/10 5-15
Softening point °c ASTM D36 °C 85-95
Ductility @ 25°c ASTM D113 cm 1.5 Min
Loss on heating(wt) % ASTM D6 wt % 0.2 max
Flashpoint °c ASTM D92 °C 250 min
Solubility is CS2(wt) % ASTM D4 wt % 99.5 max
Spot test A.A.S.H.O.T102 - Negative
For more information, please Contact our Sales Team.